Nowadays, increasingly often, metals are used in furnishings to give a sophisticated touch to the design. Sometimes it is enough to add a detail to brighten and adorn forms, creating a sophisticated look.
Metal has always been used in architecture for furnishings, even on an urban scale. Just think of wrought iron, which was popular in the past and has now been replaced by higher performance metals such as steel and aluminium. In the Middle Ages metal elements were already used in furnishings, for instance on chests where the lock is a decorative element, and in some cases highly ornamental, and on the iron heads of nails, also a decorative element, as well as necessary for assembly.
Nowadays, in addition to its aesthetic qualities, metal is used due to its long-lastingness and because it is easy to clean.
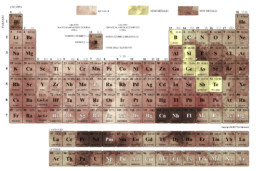
Periodic table of elements subdivided into metals, non-metals and semi-metals
Properties of metals
They can be divided into three categories:
- physical-natural: depending on the chemical-physical makeup of the material;
- mechanical: ability to withstand mechanical stress;
- technological: the predisposition of materials to be processed
Physical-Natural properties
Mass density, expansion due to heat, melting point, electrical conductivity, thermal conductivity, resistance to corrosion
Mechanical properties
Hardness, fatigue strength, tenacity or resilience, pullout strength, crushing strength, stiffness, torsional strength, shearing resistance
Technological properties
Fusibility, malleability, ductility, weldability, hardenability
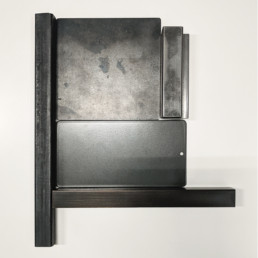
Metals used in furnishings
In the world of furnishings metals are used to produce entire pieces of furnishing as well as to add a touch of light and elegance.
Principal metals used today are: steel, bronze, aluminium, brass and copper.
Steel
Steel is an iron and carbon alloy: low-carbon or soft steel is also called iron.
This metal should be given a specific anti-rust treatment such as painting, lacquering, enamelling, chrome-plating or nickel-plating.
Stainless steel is an alloy of iron, nickel and chromium. It is harder to process but, unlike normal steel, it does not require any particular protection.
Bronze
Bronze is an alloy of >70% copper and tin, used since ancient times given its machinability and hardness. Increasing the tin content increases its hardness but also its fragility and sonority. Bronze is a brownish red colour due to the presence of copper.
Alloys containing less than 50% of copper are white, while if they contain between 50% and 95% of copper they are yellow.
Aluminium
In nature this material is never found pure but always in the form of an oxide. It is malleable and ductile, and can conduct electricity and heat. It may have different finishes. It is a silver grey colour.
Brass
Brass is a copper and zinc alloy, which may also contain various amounts of other elements such as manganese, iron, aluminium, or tin, which improve its mechanical properties and resistance to atmospheric agents.
The principal properties of brass are hardness, resistance to corrosion and machinability. It is yellow.
Copper
This metal is found in nature as a sulphuretted and oxygenated compound and, in some cases, in its nascent state. Its principal characteristics are: ductility and malleability, thermal and electrical conductivity and easy alterability in the presence of moisture. It is red but its colour may vary depending on its degree of oxidation ranging from brown to green. The surface protective patina produced by oxidation protects the material from corrosion and is often artificially recreated to produce given aesthetic effects.
Depending on its characteristics each metal can be given different finishes.
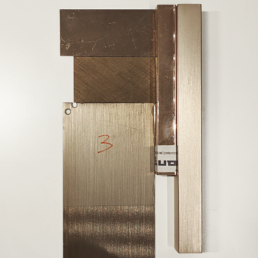
Surface finishes
Surface finish processes can improve the appearance of metal artefacts to suit project requirements. It is essentially a matter of working on the material’s reflectance. Appropriate and prevalently mechanical type treatments can produce surfaces with specular, diffuse and semi-specular reflection.
We can distinguish between two broad categories:
- mechanical finishes: sandblasting, shot blasting, axhammering, brushing, satining, buffing, grinding,
- electrochemical finishes: electropolishing, electrolytic baths
Satining
Satining is a type of finish which renders the product to which it is applied less delicate. In addition this treatment conceals any surface flaws and marks left by other treatments.
Satining is done with three dimensional abrasives such as bear-tex, scotch-brite or surface conditioning.
Sandblasting
Sandblasting is a process that can remove particularly tough encrustations, such as rust or paint, by using abrasives to polish up a surface without damaging it.
There are various types of metal sandblasting:
- white metal blasting: this entails the complete removal of all rust residues, all mill scale, all traces of old paint and, in general, all impurities from the metal surface. The process produces a uniform grey white metallic surface with enough roughness to allow successive coats of protective paint to adhere to it.
- near-white metal blasting: this entails the complete removal of all impurities from the metal surface (smithsonite, rust, dirt, old paint, etc.) with the exception of very slight shades or traces of veining, discolouration caused by rust stains, smithsonite oxides or slight lingering residues of paint or protective coating.
- commercial sandblasting: this good but not perfect treatment usually means the removal of all rust, smithsonite and other foreign materials from the metal surface. The resulting surface will not necessarily be uniform because any differences in the initial conditions of the surface will influence the end result. It will anyway be rough and therefore adhesive enough for successive coats of paint to be applied.
- brush-off blasting: this process removes loose rust scale, mill scale and paint while harder to remove traces mean paint will adhere well to the blasted surface
Shot blasting
Shot blasting is a mechanical process that consists in peening the surface with a jet of metallic grit blasted at high speed and at great force.
Axhammering
Axhammering is done when metal is cold on objects made of copper, brass, bronze, gold etc., for the purpose of decoration. The object is struck with the axhammer to produce finer and more varied results than those produced by peening.
Brushing
Brushing is done with special brushes or sandpaper and removes all impurities from the metal. Any small flaws are removed or disguised to produce an attractively smooth, even surface.
Satining
This process glosses the surface of an object so that the object in question shines with reflected light. Satining metals prepares them for actual metalworking processes such as chrome-plating, gold-plating and silver-plating and in the case of stainless steel it can provide an end solution.
There are two distinct and separate techniques techniques:
- controlled abrasion of the surface, by means of a very finely grained and uniform abrasive paste which effectively reduces surface roughness (as in the case of gems or cut glass);
- the use of waxy substances (usually with a high degree of refraction) which fill micro-asperities to give the impression of a smoother surface (like floor wax).
Buffing
Buffing is one of the many mechanical processes used to finish surfaces and is useful for finishing materials. More precisely buffing is an initial phase in the process of rough-cutting and removing sharp edges and burrs or smelting, pressing or welding residues. It is done with sanding belts and flap-wheels using semi-automatic machines or manually.
The process initially uses large grain abrasives and then increasingly smaller grain abrasives to produce the desired degree of surface roughness.
Electropolishing
This process can be applied to stainless steel products and consists in the selective removal of metal in the anodic phase. Polishing is a surface finishing process which removes material by means of electrical current. This process is particularly efficient at removing asperities and irregularities found on metal surfaces.
Electrolytic baths
Electroplating is a technique used, mainly in industry, to coat a non precious metal with a thin layer of more precious or nobler or passivable metal by means of an electrolytic bath.
For instance, electroplating can be used to coat copper with silver or steel with zinc, tun, nichel or chrome.
This process takes place in a bath containing a watery solution of metal salts that are deposited on the surface to be treated. Two electrodes are immersed in the bath: the cathode is composed of the surface to be coated while the anode may be composed of the metal to be deposited. Technical electrolytic treatments include zinc coating, copper coating, stainless steel electropolishing, nickel plating, chrome plating and others. Decorative electrolytic treatments include various types of nickel plating, chrome plating, gold plating, silver plating etc.