Wood has always been one of the most popular floor coverings due to its traits and its aesthetic appeal. Numerous varieties of wood are used (e.g. durmast, walnut, cherry, acacia, ash, etc.) and each can be given a different finish (varnished, oiled, bleached, etc).
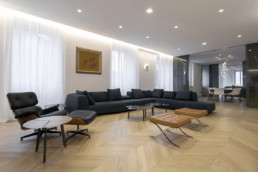
There are two principal types of wooden flooring: unfinished (solid) and prefinished (engineered).
Unfinished
Wood flooring consisting of solid wood blocks of different sizes depending on the pattern laid. The wood is varnished and treated after it is laid, in situ, and can be 22 mm thick with a length ranging from 220 mm to 2000 mm.
It can be glued onto blocks of cement, wooden panels, preexisting floors of ceramic, marble or supports that are nicely compact and resistant to traction. It should settle in approximately 15 days, depending on the wood species and type.
Characteristics:
- Damaged elements can be repaired
- Dimensional stability (shrinking or swelling): depending on the wood species used
- Maintenance: as well as standard cleaning specific treatments should be used periodically in order to polish the floor and protect it from atmospheric agents
- the protective layer can be replaced
Multilayer
This consists of two large groups: prefinished (engineered) and presanded flooring.
Prefinished
Parquet made of blocks which have been treated and varnished in the factory. The blocks have a layer of underlay, usually made of wood which is not precious but resistant, e.g. Swedish pine, fir or birch; and a layer of tread in hardwood. A good multilayer parquet has blocks which range in thickness from 7 to 15 millimetres consisting of 6-10 mm of wood underlay and at least 2.5 mm of hardwood.
The length of the blocks can vary and, in particular, prefinished blocks consisting of two layers can be up to 3-4 metres long, a length that cannot be achieved with traditional parquet flooring.
Because they are prefinished in the factory, and not in situ, the blocks can undergo a range of processes, such as distressing, darkening by means of drying and heat, fibre brushing (which produces a rough texture), hand planing, ageing (for a weathered effect) and many others.
In addition, prefinished parquet can be repaired and, for this reason, it is advisable to purchase and store a small quantity of material in addition to the amount needed for the initial laying.
Characteristics
- Quick to lay
- Damaged elements can be repaired
- Dimensional stability (shrinking and swelling): The layering of woods gives the blocks greater stability
- Maintenance: as well as standard cleaning, specific treatments should be used once in a while in order to polish the floor and protect it from atmospheric agents
Presanded
Presanded parquet differs from refinished parquet due to its lack of a finish. This characteristic means it lends itself to being finished in situ and customised.
Finishes
Once the type of block is chosen a finish needs to be chosen so as to define the look of the parquet.
Varnishing:
This creates a solid film on the parquet. The film is produced with artificial or natural resins. Varnishing can be glossy or matte depending on the gloss number (unit of measurement of the degree of opacity of a varnishing product). However, the final effect will be less natural than an oiled finish. Varnishing can produce a surface which is easier to clean and scratch-resistant.
Bleached parquet: This is natural parquet to which a white shade is applied. The hue and tone of white varies depending on the density, quantity and quality of the treatment used.
Wax treatment:
This consists in applying layers of transparent or lightly coloured substances (paste for a finish and liquid for maintenance) with brushes or rollers. Once the layers have been applied the wood is polished. This treatment does not last and must be repeated in due course. However, it is this treatment that produces the most natural looking wood
Application of oils:
Special oils for wood, dispersed in water or dissolved in organic solvents, preserve the original look of the wood and are applied with rollers or brushes.
Distressing
This can be done to flamed wood in one of two ways:
1. The wood is lime-washed and then put in kilns so that the grain stays a lighter shade compared to the rest of the block. This procedure is quite complicated and more costly than the second method.
2. First the wood is varnished (or oiled) and then it is brushed so as to produce the same effect as that mentioned above. This method produces a white grain on a darker background.
Brushing
Brushing is a treatment used to finish the surface of wood flooring with the aid of special rotating brushes. This technique produces a texture that feel rougher as the action of the brushes brings into relief the wood grain.
Flat-sawn parquet
Flat-sawing is a mechanical treatment that makes the first cut on a tangent to the circumference of the log and each additional cut parallel with the one before, using a bandsaw. If the wood is pigmented the flat saw treatment is accentuated.
Unstructured parquet
The surface of the wood is placed under mechanical stress in more than one direction. The result resembles a canvas as the wood, despite transparently revealing its true nature, appears to be composed of many micro elements.
Planing
Planing can be done manually or mechanically, producing different results. Hand planing is often recognisable due to the greater randomness of the planing and the presence of planing stops. Mechanical planing can be longitudinal or perpendicular to the wood grain. Normally technical planing produces a more regular effect.
Heat-treated parquet
The wood is treated at temperatures ranging from 190°C upwards, transforming its matter and thus altering its characteristics. It turns darker, taking on various hues, and is more dimensionally stable and slightly more fragile but more resistant to compression. To be considered as such heat treatment must be applied throughout the thickness of the hardwood. If the wood is scratched the colour underneath the scratch is invisible, unlike with coloured parquet.
Evaporated parquet
The wood placed in a drying kiln is treated with jets of steam. A chemical reaction takes place that is proportional to the content of tannin in the wood. This gives the wood a characteristic, warmer and more pleasant shade. Evaporated wood is considered as such when evaporation penetrates the thickness of the hardwood. If the wood is scratched the colour underneath the scratch is invisible, unlike with coloured parquet.
Smoked, fumed or plate -heated parquet
Smoked , fumed or plate-heated parquet can be treated with a combination of the above-mentioned evaporation or heat-treatment techniques. Treating the surface with plates instead produces an irregular scorched effect due to the repeated contact with very hot metal surfaces.
Sometimes in the trade the name Parquet Fumé is used to describe a treatment using ammonia. As well as producing blocks of mismatching hues this treatment is not environmentally sustainable.
Manually aged or antiqued parquet
This treatment gives the wood a uniquely uneven shade and look. Ancient wood flooring should not be confused with flooring obtained by means of antiquing. The antiqued effect is produced using rollers with uneven bristles, various mechanical treatments and/or treatments with chemical reagents.
Choice
Regarding the pattern and grain of wood: blocks without knots are considered to be more precious than blocks with knots. Woods are classified in accordance with European regulations UNI EN 13489
●(Class 1) ▲ (Class 2) ■ (Class 3)
UNI EN REGULATIONS
IDENTIFICATION OF CATEGORIES AND SYMBOLS | ||
SYMBOL | CATEGORY | OUR REF. |
● | Class 1 | First |
▲ | Class 2 | First comm.le or Std |
■ | Class 3 | Nodino or Nature |
UNI EN REGULATIONS Quality classes for wooden elements of oak (Oak) |
||||
Faccia in vista dell’elemento | FEATURES | CLASS ᴏ | CLASS Δ | CLASS □ |
Healthy sapwood | Not allowed | Allowed (*) | Slight traces allowed | |
Healthy and adherent knots b<70 mm Rotten knots b=70 mm |
Allowed if: diameter <= 2 mm Not allowed if diameter <= 3 mm |
consentiti se con diametro: <= 5mm <= 10mm<= 3mm |
Allowed if with a diameter: <=15mm <=30mm<=10mm |
|
Splits | Not allowed | Allowed | All features are allowed with no size or quantity limits if they do not compromise the strength or wear resistance of wooden floors |
|
Inclusion of bark | Not allowed | Not allowed | ||
Lightning strike | Not allowed | Not allowed | ||
Deviation of the grain | Allowed, no limits | Allowed, no limits | ||
Colour variations | Slight variations allowed | Allowed (**) | ||
Ray parenchyma | Allowed | Allowed | ||
Biological alteration | Not allowed | Not allowed | Not allowed, except for fungi and insect damage |
UNI EN REGULATIONS Other broadleaf trees |
||||
Faccia in vista dell’elemento
|
FEATURES | CLASS ᴏ | CLASS Δ | CLASS □ |
Healthy sapwood | Not allowed | Allowed | Slight traces allowed | |
Allowed if diameter <= 2mm not grouped diameter < 1 mm not grouped |
Allowed if diameter <= 5mm not grouped diameter <= 2mm not grouped |
All features are allowed with no size or quantity limits if they do not compromise the strength or wear resistance of wooden floors |
||
Splits | Not allowed | Allowed if they do not run through the element, that is with a width = 0.5% of the total length of the element |
||
Inclusion of bark | Not allowed | Not allowed | ||
Lightning strike | Not allowed | Not allowed | ||
Deviation of the grain | Allowed without limits | Allowed without limits | ||
Colour variations | Slight variations allowed; Slight traces of natural discolouration and mineral striations allowed |
Allowed | ||
Ray parenchyma | Allowed | Allowed | ||
Biological alteration | Not allowed | Not allowed | Not allowed, except for fungi and insect damage |
From the circle to the square parquet choices range from straight grain to “wavier” grain to rustic grain. Regulations are adapted to different tree species.
Laying parquet
Fixing
The parquet is glued onto the screed. It is an ideal method for all sizes of parquet. Just the right amount of glue is spread with a spatula . A join encircling the perimeter of the room allows the wooden floor to expand naturally when hygrometric conditions vary.
Fixing of prefinished floors
Specific types of glue must be used for prefinished floors as the blocks are prevarnished and so there is no margin for error. Cleaning is essential during the processing of prefinished floors as any traces of glue could damage the material that has already been varnished.
Floating
The floor is rested loosely on the ground, on top of special felt (expanded polyethylene, cork etc.) with a thermal and/or acoustic isolation capacity. Perfect for laying large three layer blocks, it also guarantees soundproofing and provides a barrier against humidity. For this type of laying the screed must be perfectly level to prevent blocks from shifting and clattering. It is only suitable for some types of prefinished flooring with interlocking elements. The blocks are laid by resting them on the levelled subfloor and on a sandwiched layer of male-female sound proofing insulation. The elements are fixed by means of a thin layer of vinyl glue applied at the point where the blocks interlock.
Nailing or screwing
This type of laying is done with solid wood planks with edges of a thickness of 20-22mm. The nails are driven in at 45° to the tapped part of the block to a depth of approximately 20mm in the subfloor. The particularity of this type of laying is that the blocks creak when trodden upon. This creaking can be reduced by means of screwing the blocks. In any case the heads of the nails or the screws must be invisible. The support must be suitable for laying with nails and screws. Principal types of support are : nailing strips, wooden boards and joists that are rested on or are part of the subfloor.
Laying patterns
The juxtapositions of elements that make up a floor generate a pattern which is called a laying pattern.
Principal types are:
Shipdeck
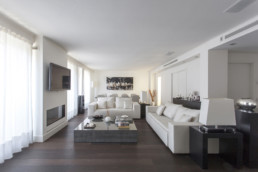
The single blocks of differing lengths are arranged lengthwise so that the butt joints are positioned irregularly. It can be done by placing the blocks parallel with or diagonally to the wall. In the first case it is best to place the blocks perpendicular to the main light source so as to reduce the visibility of the joins. Before starting to lay the parquet it is important to check that the walls are square. In the second case the elements are generally laid at an angle of 45° or 30° to the walls, starting from the entrance door and moving in the direction of the main light source, or towards the end of the room. Unlike straight laying this method conceals any walls which are obviously out of square.
Regular deck
This method of laying, which was popular in the past, differs from the former method only in that the individual elements are arranged lengthwise, so that the butt joints are positioned at the same midpoint or anyway at the same spot as elements in the previous row. The wooden blocks that make up the pattern must all be of the same length.
Herringbone
The individual elements are arranged at 90° angles, in parallel rows and so that the end of each block is joined to the end of the next block. Herringbone laying can be done in two ways: straight and diagonal.
Large rooms are most suited to this pattern as it tends to make the room look smaller. This type of laying also produces the pleasant sensation of having used woods of different shades thanks to the light striking the floor at a different angle.
Chantilly/Versaille
The edges of the flooring are formed of blocks laid differently to the central part and blocks that interlink with the different patterns. The blocks can be of different woods to create special effects.
French herringbone or Chevron
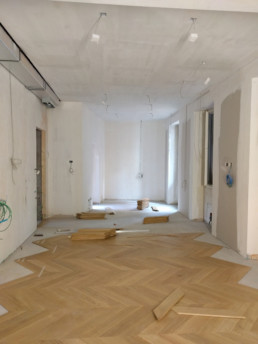
The single blocks are laid at angles of 45° or 60° to each other to produce a parallelogram and not a rectangle. The method of laying is the same as for herringbone.
Mosaic patterns
Blocks are assembled to form a square. Mosaic patterns do not conceal walls out of square. The squares can be laid within a border with interlocking blocks. The result is a highly decorative flooring suited to spacious and representational spaces.
Factors affecting cost:
– Type of wood used
– Choice: ● (circle) ▲ (triangle) ■ (square)
– Finish: e.g. satining, shot-blasting etc.
– Thickness of the layer of hardwood: ranging from 2.5 to 6 mm.
– Number of layers: three layer is more expensive than two layer prefinished parquet but also more stable with regard to variations in temperature and dampness.
– Length of block: the longer the block the higher the price. Blocks can reach up to 3 metres in length but starting from 2 metres costs are quite high.
– laying pattern.